A battery testing and research company backed by Australia’s St Baker Innovation Fund, and with links to Tesla’s exclusive battery research lead Jeff Dahn, has patented a new single crystal cathode process that could dramatically reduce the cost of making lithium-ion batteries.
Novonix sprung out of Tesla battery researcher Jeff Dahn’s lab at the Dalhousie University, and as reported by The Driven on Friday sponsors the work of Mark Obrovac at Dalhousie.
Founded by Novonix co-founder and ex-Tesla senior battery engineer Chris Burns and former Jeff Dahn research associate David Stephens in Canada in 2013, its managing director is Australian entrepreneur Philip St Baker.
He is the son of Trevor St Baker, the prominent coal baron who also formed the St Baker Energy Innovation Fund that has provided significant funding for Australian EV charging companies Tritium and Evie Networks, and other solar and battery technologies.
Shares in Novonix surged when rumours emerged in early June that a partnership may be in the offing between Tesla and Novonix, which has just commercialised a dry particle microgranulation (DPMG) that could reduce costs, waste, and environmental impact of materials used for anode and cathode production.
Now, its stock has surged again, almost doubling to reach $1.31 at the latest market close following news that it had patented a process using the DPMG technology to make a single crystal cathode, and would move into a pilot to produce the cathode on a small scale with a view to commercialisation.
Single crystal cathode technology is now the benchmark for best-in-class lithium-ion batteries, doing away with the traditional polycrystalline structure of battery cathodes that are prone to cracking and damage as a battery is discharged and recharged over time.
A Tesla single crystal cathode patent has brought considerable attention to the topic, with the significance of its unique two-step process to create a high purity cathode explained here.
But while Tesla’s patent – which has been widely publicised by Dahn as a major step towards achieving a battery that can last a million miles – addresses the challenges of creating a high purity single crystal cathode material, Burns says that with DPMG technology, a single crystal cathode can be created more cheaply and with better performance.
“We’ve filed a patent previously around DPMG and its uses to make spherical graphite materials as well as cathode materials,” says Burns.
“What we’ve announced this week is that from that work … we immediately started working on how we could use the technology to make single crystal materials.”
As Burns points out, there are several car manufacturers currently seeking to utilise long-life battery technology now commonly known as a “million-mile battery”. Such batteries can cycle 3,000-5,000 times, and will drive further adoption of electric vehicles and energy storage.
“They’re more robust particles, as traditional material can have cracks,” he says. “We’ve seen in cycling programs we’ve run here that these single crystal materials can really enable longer cycling performance than polycrystalline counterparts.”
“What Dr. Obrovac did was try to get the cost of the battery down and the make life of the battery longer,” he says.
To do that, Novonix is applying its DPMG method to making single crystal cathodes in the hopes to proffer a cheaper, and well, less messy, way of making what is the most expensive part of a battery.
“We can use a completely different process [to Tesla’s patent]- with dry particle technology, no solvents and other such materials are needed.”
While there are many mass produced single crystal materials already on the market, Burns says Novonix is benchmarking those currently available products in order to keep one step ahead.
“We’re moving the benchmark a little bit at a time. We believe it can be done through a much easier and cost effective methodology and make particles that look exactly the same,” he says.
Now, Novonix is looking at how to scale up production, demonstrating how it would look as a commercial product – and how much it would cost to produce per kilowatt hour.
“We’ve proved we can make materials that work – now the question is how to make them best in class.”
Correction: This article has been edited to clarify the fact that Novonix is not funded or backed by Tesla. Novonix researcher Mark Obrovac works at the same university as Jeff Dahn and co-founder Chris Burns used to work for Tesla. The two companies have separate patents on single crystal cathode processes.
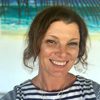
Bridie Schmidt is associate editor for The Driven, sister site of Renew Economy. She has been writing about electric vehicles since 2018, and has a keen interest in the role that zero-emissions transport has to play in sustainability. She has participated in podcasts such as Download This Show with Marc Fennell and Shirtloads of Science with Karl Kruszelnicki and is co-organiser of the Northern Rivers Electric Vehicle Forum. Bridie also owns a Tesla Model Y and has it available for hire on evee.com.au.