I reported last week on engineer Jon Edwards’ progress in preparing his Hyundai Mighty for the first lap of Australia in an electric truck, starting in Perth.
Jon originally planned to do the trip in a Mitsubishi Fuso truck he is converting to electric using a Tesla battery and motor, hence the nickname “Fusla”.
I also reported on this conversion in September 2023 but much has changed since then and the Fusla has become the more challenging and perhaps more interesting of the two projects.
The Fusla’s tray has been raised sufficiently for the 75kWh battery to sit under it, well protected from the road and debris, with the battery coolant running through the original Tesla plumbing to the repurposed intercooler from the original diesel motor, placed under the tray.
The 310kW Tesla Model S AC motor, inverter and differential are positioned sideways under the cab. The differential has been locked and re-geared to roughly double the torque delivered to the rear wheels of a nominally 5 tonne vehicle.
This will also roughly double the engine’s RPM for any given speed compared with the Tesla S but should not affect efficiency too much.
The motor, inverter and battery penthouse are cooled using the truck’s original radiator and original Tesla plumbing. It all fits very neatly and is easily accessible by lifting the hinged cab forward.
The vacuum pump for brakes and steering pump (ex Holden Astra) run off the 12V battery and the air conditioning is powered from the main battery via a 400V junction box with a separate control board.
The really clever bits are the controllers for the motor and battery. These are after-market black boxes from EV Controls (www.ev-controls.com) which replace the Tesla computer, hack directly into the Tesla system and transmit data via
Bluetooth to an iPad neatly embedded as the new instrument panel. The EV Control app configures the screen which is beautifully functional.
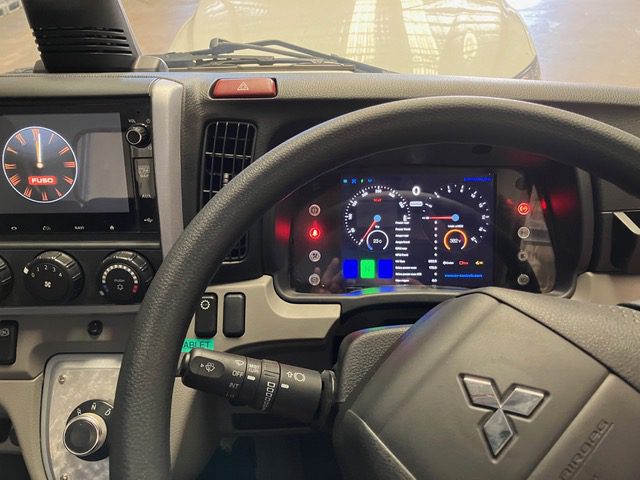
The “motor” screen (see pic) is required to drive the truck and the “battery” screen can be displayed on any Apple Bluetooth enabled device to turn the battery on and to display its parameters. In a nod to the old ways, the keyed ignition on the steeringcolumn needs to be turned on to drive the truck.
The metal protective cover over the battery penthouse initially blocked the Bluetooth signal, so Jon has installed a “Ned Kelly” perspex window.
The Tesla accelerator and throttle system are wired to be inactive if the brake pedal is in use. The gear shifter is replaced with a knob which is interlocked to prevent selection of drive or reverse modes when the hand brake is on.
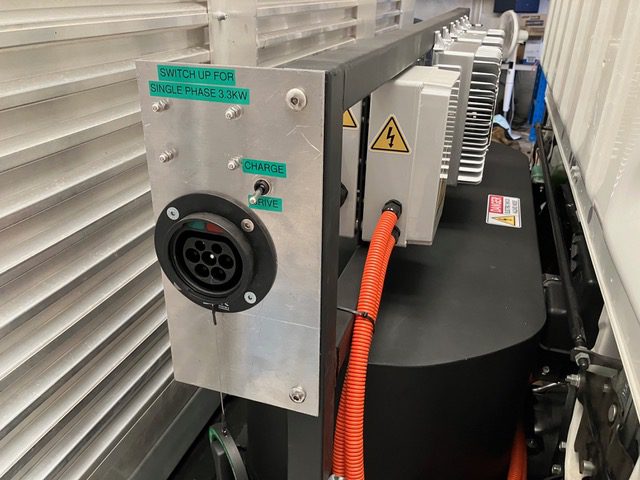
Jon has completely changed the truck’s charging system, ditching the planned hard wired Biofil generator. The used Tesla 75kWh battery came with a non-functional CCS2 port, so Jon has installed a type 2 plug which supplies 6 air cooled 3.3kW 400V DC chargers hard wired to the battery.
This setup will charge at 20kW from a 32A 3 phase plug and can be switched to draw only 3.3kW from a single phase 15A caravan outlet.
It will also be possible to charge at 20kW from a standard type 2 charger with installation of the hardware to allow the truck to communicate with the charger via the two comms ports at the top of a type 2 plug. This is under way.
Jon is hoping for a range of around 200km but still retains the option of extending this by carrying a 20kW Biofil generator and some used chip oil, providing he stays off the social media platforms as they arc up.
In all, this is a really elegant conversion using tested components in clever ways, such as the approach to management of battery/engine temperatures, the Bluetooth solution and the robust and simple charging system in the absence of a CCS2 port.
Much thought has gone into the design and conversion of a vehicle which appears to be well suited to a lap of this often harsh and unforgiving country.
Note: The Fusla will be on display and Jon will be talking at the AEVA workshop on Saturday, April 20, at the Canning River Eco education centre, Cannington.