We are encouraging questions from readers about electric vehicles, and charging, and whatever else you want to learn. So please send them through and we will get our experts to respond, and invite other people to contribute through the comments section.
Our latest question comes from Steve, who asks:
I’m planning to get an EV soon-ish, hopefully within the next 12 months when there are some decent options. The Kona appeals to me the most, but I was wondering about the high cost. Currently the top-of-the-line ICE Kona Highlander (1.6L turbo+DCT) costs just under $A41,000 drive-away, and early intel indicates that the EV will probably cost $A54,000 + on-road-costs.
Based on what little information I can find about costs per kWh to package a battery, it seems that the 64 kWh battery in the Kona would cost between $A14,000-$A18,000, which if accurate accounts for the difference in cost between these models. The extra safety and comfort tech appear to be identical across the two models, so it should be a fair comparison.
What I cannot reconcile is that I would expect that a simple electric motor must be easier and cheaper to produce than a complex ICE engine and drivetrain with its very many moving parts in the engine, turbo-charger, dual-clutch transmission, rear differential and AWD diff.
How is it that the EV costs so much more than the ICE, even taking into account the expensive battery? I saw a video a couple of days ago where they said that a EV engine manufacturer was producing an engine, transmission and power electronics package for around $A2500, would it cost about the same for ICE and drivetrain?
 Can you shed any light on this?
Our resident expert Bryce Gaton, from the Australian Electric Vehicle Association, responds:
Hi Steve – you have asked, albeit in a rather more nuanced fashion, the eternal intending Electric Vehicle (EV) owner’s question: just when will EVs be affordable to the mainstream buyer?
The answer comes in several parts.
The first part relates to spreading the development costs. 100 plus years of uncountable billions of development dollars (and hours) have gone into refining the internal combustion engine (ICE) and the associated gearbox needed to maintain the motor within its most efficient torque range.
These both are now at a highly developed pinnacle, and produced in the tens of millions a year. Spreading the development costs across each ICE motor/gearbox combination makes those costs per unit quite low.
The second part relates to the raw material supply chain.
Again, 100 plus years of building an iron ore extraction, smelting, casting and panel stamping industry to build car bodies, motors and gearboxes, plus the oil to lubricate them and burn in them has come up with a well-oiled machine (pun intended) to easily and quickly produce all the components to build and run an ICE car.
EVs require many of these systems too – production of steel for bodies, iron for electric motor cores, copper for motor windings are all well established, as well as the manufacturing capacity for each.
However, neither battery raw material extraction/refining or battery-pack production capacity are anywhere near the levels needed for full-scale replacement of the fossil fuel supply chain.
That is still building up – and is in fact the biggest hurdle in producing EVs in the numbers needed to meet the pent-up demand for them from the public.
The third part relates to the concept of ‘the economies of scale’ alluded to in the previous two parts.
With a very mature supply chain to produce the resources and components cheaply, PLUS a century and more to spread the development costs over, PLUS tens of millions of units built per year to spread the supply chain and product development costs over, and you have the current situation of a super cheap mass manufacture system for building, selling and servicing ICE vehicles at the zenith of its reign.
So now we come to EVs. They are supply constrained in terms of battery raw materials and battery manufacturing capacity, they are still built in low numbers compared to ICE vehicles so cost amortisation is higher per unit, AND the existing players are scared s#!tless by the dislocation that EVs offer to their existing cheap sale/continuing service and parts sales model.
(Kodak had a similar reaction after inventing the digital camera then ignoring the idea, even as others built them, as it would ruin their business model of selling cheap cameras and making the money on selling the films and developing them.
Lesson: cameras are still around – in far greater numbers than before the digital revolution – but the Kodak we knew is gone, and in doing so gave a whole new meaning to Kodak’s then advertising campaign slogan of ‘capturing the Kodak moment’ to the ‘Kodak Moment’ being the moment when you lose market relevance).
So the question turns around a bit as it seems that EVs are the last thing existing manufacturers want to build and the ones that are available should still be very expensive indeed.
(Given a lot of EV development work has happened in a short time and is spread over a small number of sales, plus the resource supply chain and battery construction industry are still ramping up).
The answer is that EVs are a ‘disruptor’ –the electric motor with around 17 parts replaces the ICE with 400, 500 or more parts. The EV single speed reduction gear transmission replaces those pesky (and occasionally unreliable) multi-speed gearboxes and DSG clutch systems. Together, these can reduce a vehicle manufacturing workforce by up to a third.
These savings in the vehicle’s parts and labour costs can then be offset against the currently high battery and development cost – making EVs cheaper than they could be currently expected to be – which is noted in your initial question Steve re engine/gearbox vs electric drivetrain and battery costs.
On top of this, EVs require far less servicing and have no need for the value-added consumables that feed the ICE vehicle service industry – just like digital cameras have no need for film or developing systems. No wonder the incumbent players are reportedly terrified of EVs!
Presently, numbers of EV sales (overseas at least) are increasing rapidly and battery production is being heavily invested in across the world. So costs ARE coming down, AND numbers are ramping up to spread those development etc. costs over.
Tesla is a (if not ‘the’) major driver of the change – but some other manufacturers are coming on board now they see the ‘writing on the wall’ for ICE costs being inevitably higher in the long-run and so must lose-out to EVs.
As a result of all the above, I hope you don’t mind Steve if I reframe your question as: ‘When will the tipping point be when EV prices reach that of equivalent ICE vehicles?’ One respected analyst in this field is Bloomberg New Energy Finance (BNEF). They have come up with a series of well researched reports on this topic – and whilst I am referring to their findings here, their predictions are much in line with others.
BNEF in their 2018 Electric Vehicle Report predicted that ‘the upfront cost of EVs will become competitive on an unsubsidized basis starting in 2024. By 2029, most segments reach parity as battery prices continue to fall’.
Note that in 2017, BNEF were predicting the tipping point to be 2025 (as shown in the BNEF graph below) so the date is moving ever closer!
Furthermore, it is worth noting that beyond that date EV prices will continue to trend down below ICE. At that point, I suspect that a few current big ICE vehicle manufacturers may have ‘Kodak moments’ of their own!
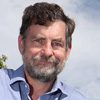
Bryce Gaton is an expert on electric vehicles and contributor for The Driven and Renew Economy. He has been working in the EV sector since 2008 and is currently working as EV electrical safety trainer/supervisor for the University of Melbourne. He also provides support for the EV Transition to business, government and the public through his EV Transition consultancy EVchoice.